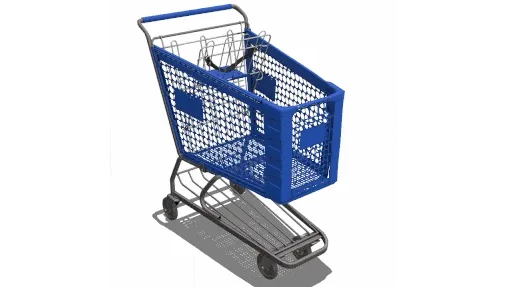
3D Model of the Month: Converting Geometry Holes to Alpha Textures with Remeshing
Optimizing 3D models for real-time applications is all about balancing detail with performance. Complex geometry can make or break a model’s usability, especially when dealing with intricate hole patterns like woven baskets, metal grids, or complex shapes like a shopping cart.
Traditionally, preserving these details while keeping poly counts low requires painful manual work - unless you take advantage of an automated solution. That’s where our Remeshing tool comes in. This post will show you how to automatically convert geometric holes into alpha textures, making your models both lightweight and visually accurate.
What is the Remeshing tool, and how does it convert geometry to alpha textures?
The Remeshing tool, also known as the Remesher, is a powerful geometry optimization method. Unlike decimation, which simplifies an existing topology, Remeshing creates an entirely new mesh based on the model’s shape, ensuring a brand-new and optimized structure.
One of its key features is the ability to close topological holes. When combined with the Bake Holes to Alpha setting, the previously geometric holes are baked into an alpha texture - allowing you to preserve the visual detail without unnecessary geometry.
How to use Remeshing for optimal results
Remeshing is a flexible tool, but getting the best results depends on adjusting the right settings. Here’s a breakdown of the key parameters:
Remeshing Method: Choose between Voxelization and Shrinkwrap. Each algorithm generates a different output mesh, so experiment to see which one works best for your model.
Remeshing Resolution: This controls the accuracy and smoothness of the final mesh. The ideal value varies based on factors in your model like hole size and hard angles. Keep in mind that adjusting your face target will also impact the optimal solution.
Bake Holes to Alpha: Enable this setting to convert closed holes into an alpha texture.
All these settings can be configured in the Web UI under your 3D Processor Presets for easy workflow integration.
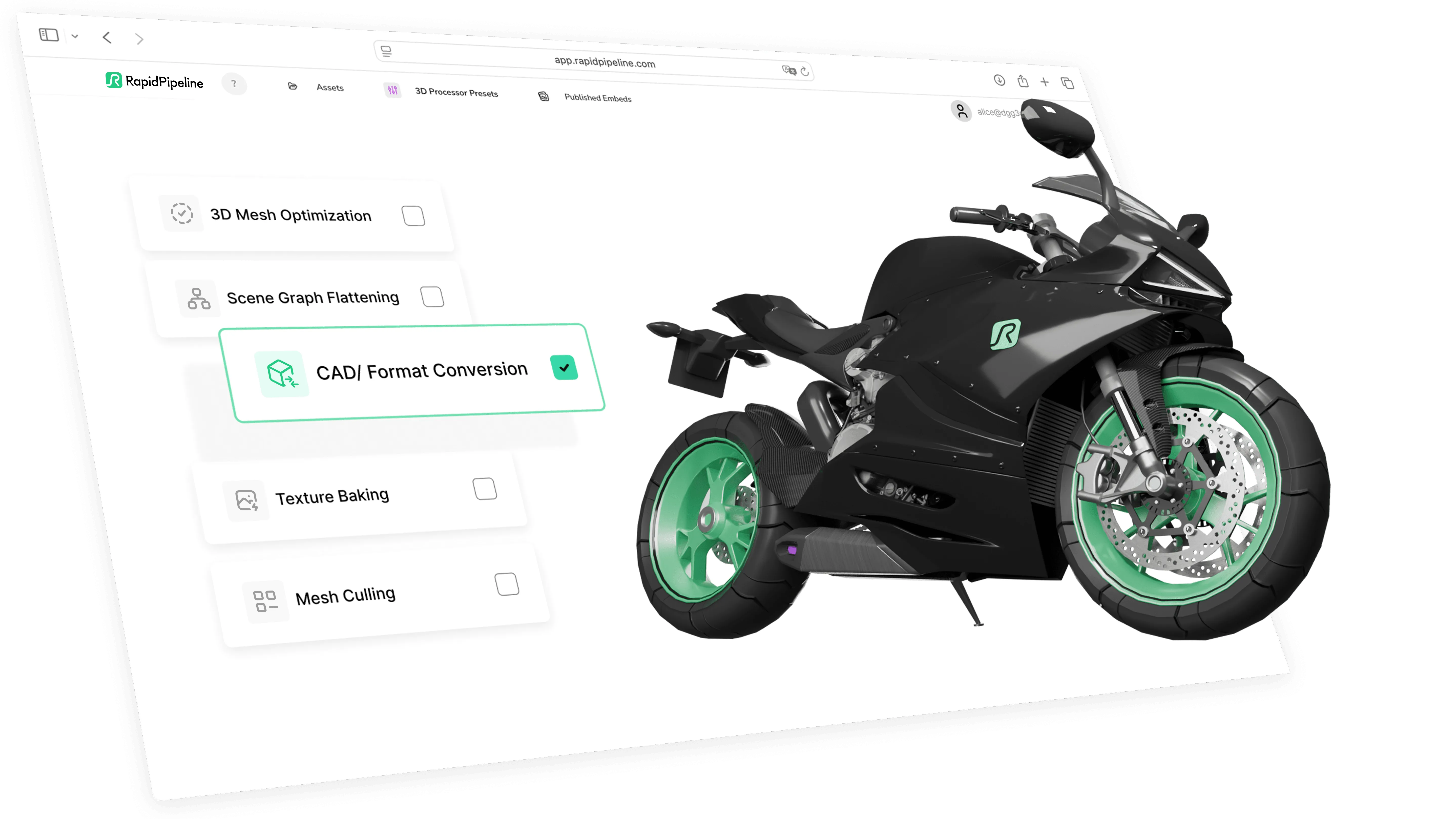
So, is it as simple as just Remeshing?
Technically, yes - but in some cases, your model will consist of different types of geometry, requiring a more nuanced approach. Let’s take our shopping cart example:
Plastic basket (blue part): This section has a repetitive hole pattern that would require excessive geometry to preserve. It’s the perfect candidate for Remeshing and Baking Holes to Alpha.
Metal frame and wheels: These elements consist of thin cylindrical structures that are spaced apart but don’t follow a hole pattern. They also are not forming a solid shape, like the basket forms a cube. Standard decimation is more appropriate here.
If we were to apply Remeshing to the entire model, the metallic parts would lose fidelity. Instead, the best approach is a two-step process. With our new Blender Plugin, processing the different parts separately is as easy selecting them before optimization. Our processing was separated like this:
Remesh the perforated plastic section to bake holes into an alpha texture.
Decimate the metal structure to optimize it while maintaining detail.
The result
By combining Remeshing and Decimation, you get the best of both worlds: a model that looks great, runs efficiently, and is optimized for real-time applications.
This method automates what would otherwise be a tedious manual task, ensuring that your hole-patterned models remain visually accurate while staying performance-friendly. Try it for free and optimize those holes in your models!
Hover your mouse or click below to be able to interact with the 3D model:
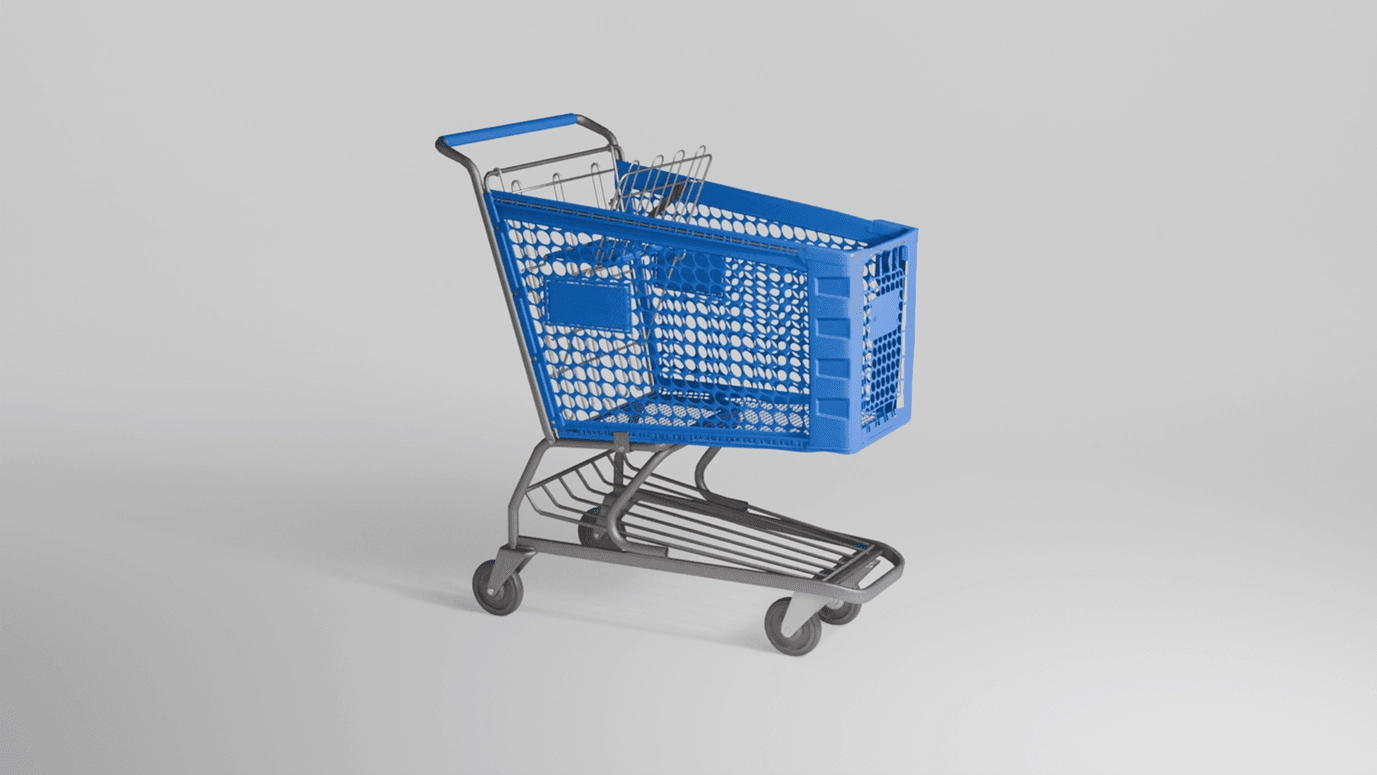
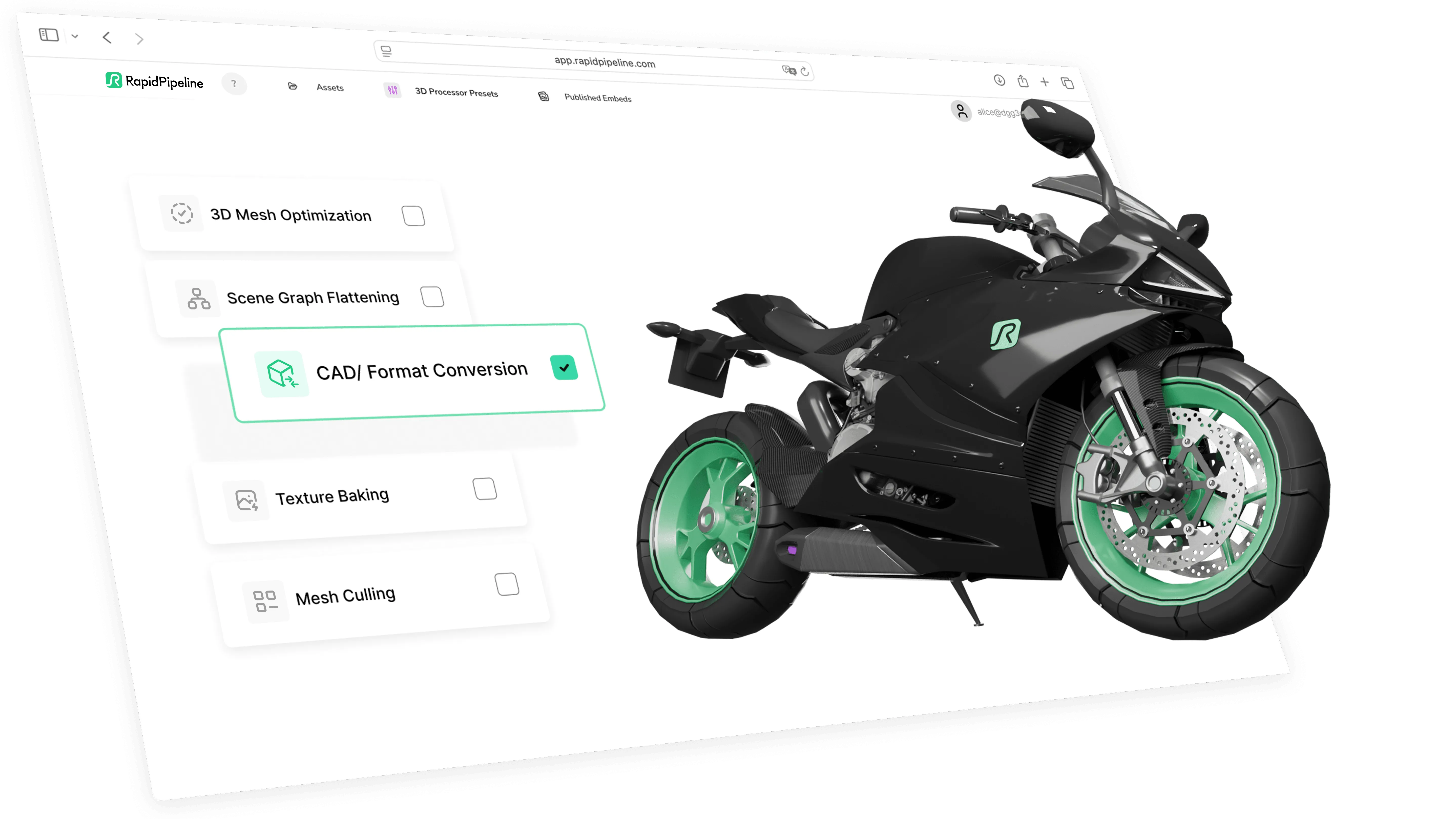
Meet the Author
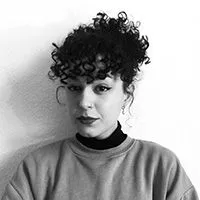
Teresa
Technical 3D Artist
Teresa is a 3D Technical Artist at DGG, bringing with her a robust background in Animation and Game design. Driven by a passion for the intersection of art and technology, she relocated to Germany to pursue her artistic ambitions. Within DGG, Teresa plays a pivotal role in infusing the team with her artist's perspective, focusing on the creation of high-quality visual content and ensuring the quality assurance of tools. Her overarching goal is to continually evolve within the industry, delivering compelling visual solutions that resonate with DGG's mission of streamlining and scaling 3D content preparation.
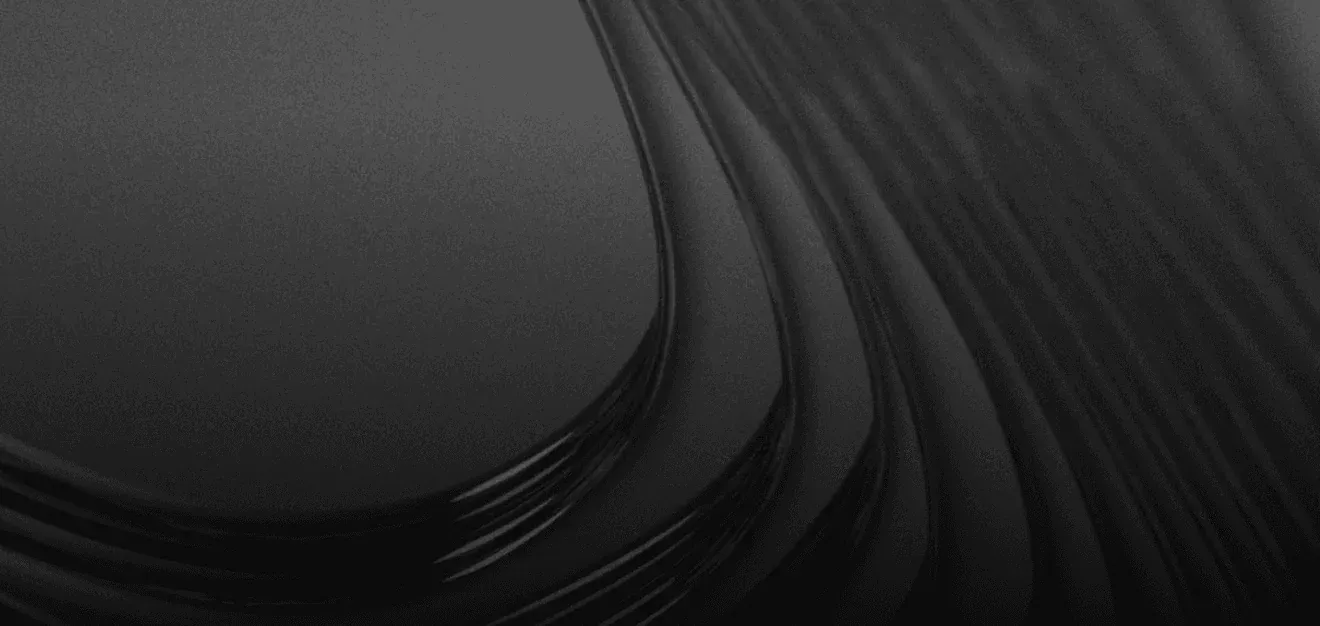